Chris and Al, the Pitt Rivers technicians working on the new Cook-voyage display, have mocked-up the case to make the process of mount making and object installation easier. Otherwise, this work would have to be carried out in the Lower Gallery, causing disruption to visitors for longer than is necessary. Only when all the mounts have been made and the objects placed according to the design, will the final installation into the real case occur.
One of the first challenges we've been working on is how to display the Tahitian barkcloth. Even though the new case is 8 metres long and nearly 3 metres high, there still doesn't seem to be much room!
In previous displays, the barkcloth has been folded, and often other objects placed on top. We wanted to recreate something of the feel of this type of display, but at the same time wanted to avoid creating deep creases in the barkcloth, which can be caused by folding them tightly. We needed to find a way to reduce the size of the barkcloth too, and reluctantly decided to omit
1886.1.1248 which at over 12 metres long was too big to fit in at all.
The solution was to roll the barkcloths over oval-shaped rolls, reducing the height of each roll, meaning that we could fit more into the space available. A section of barkcloth could extend from the roll, and be held over a padded metal bar - this is the model Chris and Al made to illustrate the concept - you can see it allows us to stack the barkcloths in a limited space but still give an idea of the different colours and designs on the cloth, as well as the sheer volume of barkcloth collected.
 |
Model of barkcloth mount |
The next stage was to make the rolls - they were constructed from zero formaldehyde MDF with inert foam edges. The rolls were covered with Moistop barrier foil and aluminium tape to seal the surface, as the barkcloth was rolled directly onto them.
 |
Ironing Moistop barrier foil onto the rolls |
Careful calculations of the space available and barkcloth sizes allowed us to sort the barkcloths into their positions in the stack. The barkcloths were rolled onto the supports, with a measured amount protruding from the roll to hand over the padded bar.
 |
Preparing to roll a barkcloth |
Once rolled, the supports could be slotted into position in the case mock-up, and the barkcloth arranged over the bars.
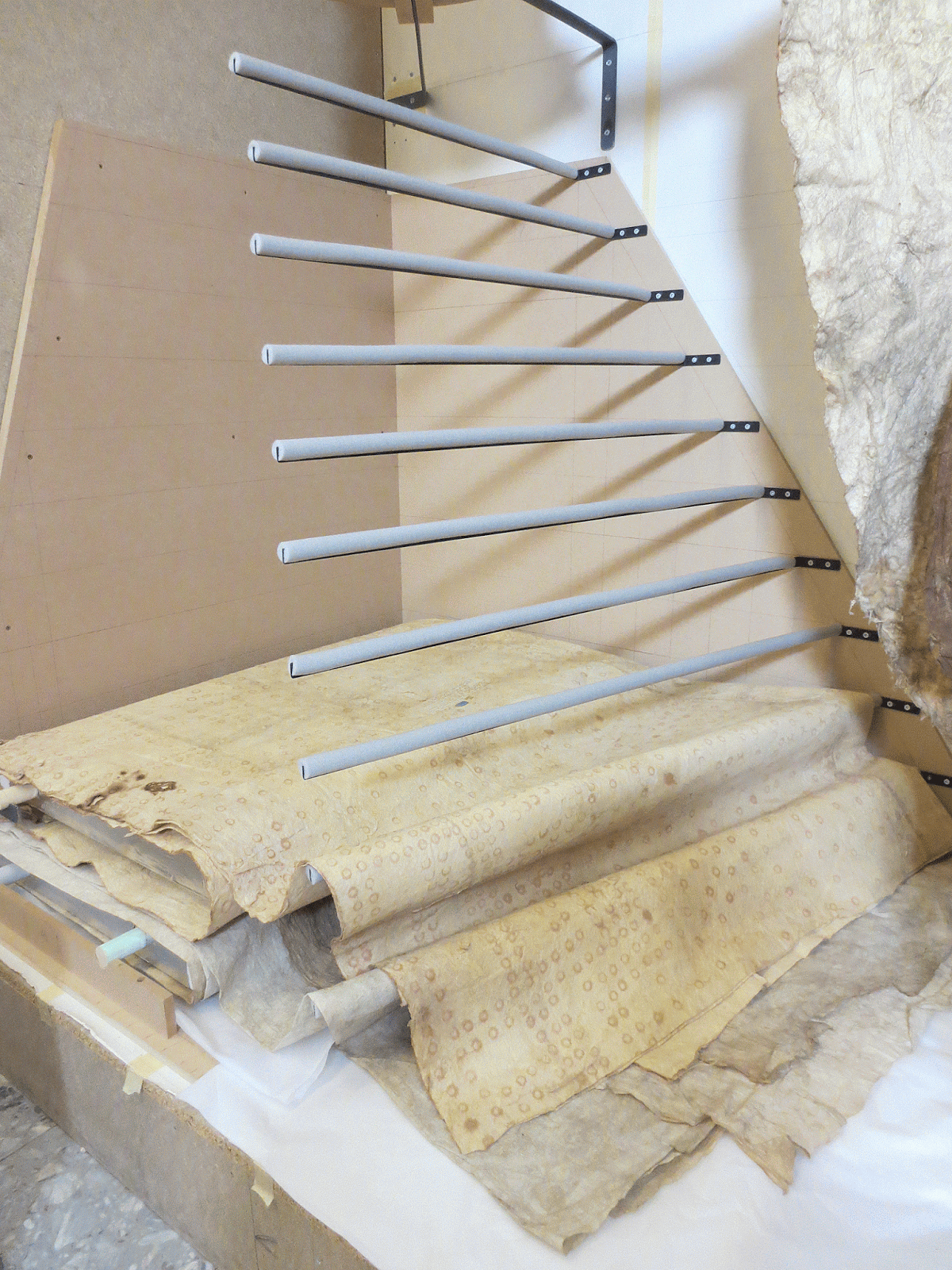 |
The bottom two barkcloths in position |